Company Overview
About Kevin's
Foshan Kevin Garment Co., LTD. was established in 2015 and is a garment manufacturer. The factory covers an area of 3,500 square meters, has 87 employees and a monthly production capacity of over 40,000 pieces. The main services are brand OEM and personalized sample customization, without the restrictions of MOQ, and it has a strong comprehensive production capacity. The main cooperative countries are Europe, America, Southeast Asia and the Middle East. We help customers produce over 3,000 samples every year and have more OEM cooperation.

Impeccable Finish
Customized Cases
Durability
8 sectoral collaboration
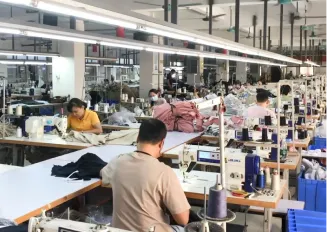
One of the most core parts of the garment factory, responsible for converting design drawings into actual finished products.
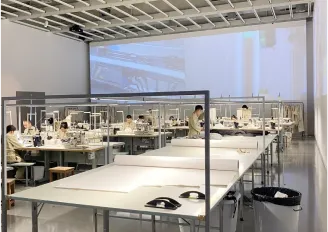
Important link in the garment factory, converting the designer’s ideas into executable templates (patterns).
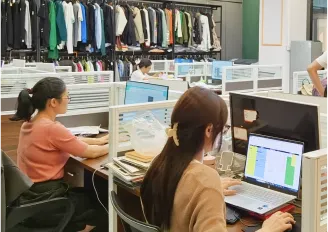
Responsible for marketing, sales and customer maintenance of the company’s products
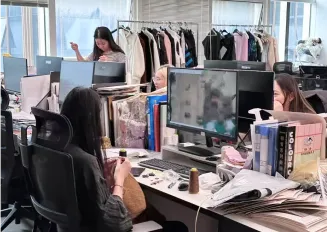
Not only involves digital marketing, data analytics and user growth strategies, but also requires cross-functional collaboration
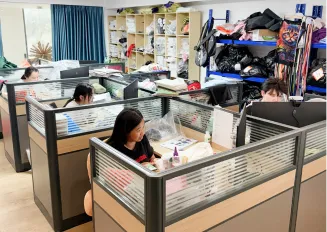
Promote product marketing and maintain customer relationship
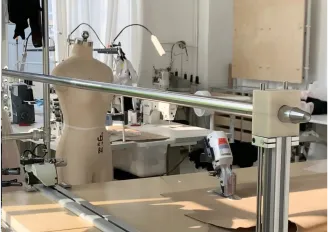
Responsible for translating market needs from visual and functional aspects into specific product designs
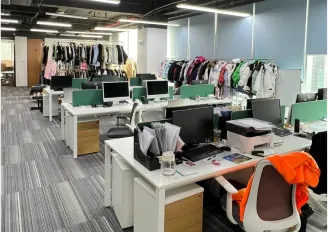
Ensure that raw materials (such as fabrics, accessories, etc.) are supplied on time and in good quality
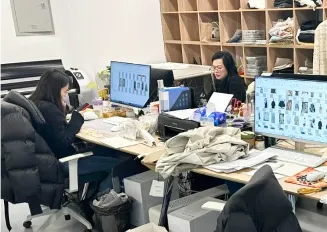
Responsible for dealing with all kinds of problems and needs of customers after purchasing products
How they do their jobs well
I’ve been in the industry for 15 years and have been exposed to many more customers.For their own position work, help customers to make products if the price, the product has been confirmed. The most important thing is to do a good job in every detail, help customers to monitor the quality of production, and the whole process of service, so that both sides can be good to cooperate.
Management of a factory will have many, many things, often have to think about to headache.1. The most important thing is that if there is a problem, it must be solved immediately, this is my idea of doing this position, 2 to ensure that each order in accordance with the time of delivery, so that customers can rest assured. There may be problems with the fabric, the product in addition to errors, or a lot of time for orders during peak times. There must be many problems in running a factory.
I strive for excellence and meticulousness in drawing every single pattern. With professional skills, I interpret design concepts precisely, laying a solid foundation for creating perfect garments.
I strive for excellence and meticulousness in drawing every single pattern. With professional skills, I interpret design concepts precisely, laying a solid foundation for creating perfect garments.My goal is to ensure customer satisfaction. I precisely control every step to guarantee the efficient execution of orders and safeguard every transaction with professionalism and dedication.
What we do to solve the common problems of our customers
1. What about employees' birthdays?
Every month, we dedicate one employee's birthday and everyone participates. It makes our work more fun. For example, we'll chat together in the conference room and have a fruit dinner party.
2.Production order staff found that the sample shrinkage rate is problematic, how to solve the problem?
Firstly check the fabric for correct shrinkage and recalculate the size. Expedite the re-sample to be completed in the time requested by the customer.
3.How is the production sequence arranged when there are particularly large orders?
There are special production meetings every week to execute the time plan of production according to the customer's required time.
4.The sample model is not up to standard, how can I fix it?
Individual staffing and time to rework and expedite production.
5.Customers need personalised fabrics or accessories, how do factories source fabrics?
According to the design drawings given by the customer and the customer's brand concept. Firstly, we provide customers with a variety of options, and finally customers determine the fabrics and accessories according to the information provided by the sales staff.
6.The production completion time requested by the customer is very short, far below the normal production time, and the customer has already placed an order. How can the factory arrange this?
First of all, we discuss the time programme with the customer first, while the factory actively cooperates to help the customer to shorten the time.
7.How to pack and ship the product after it has been manufactured?
Immediately into the quality control and packaging workshop. Commitment to the quality of the product threads and ironing of the clothes to pass, as well as packaging neat and beautiful.
8.Customers come to China to visit the factory, how the factory is arranged?
Firstly the business confirms the time to the client and then arranges the hotel and transport.